CACES® R485
(Cat 1 et 2)
Chariots de manutention automoteurs gerbeurs à conducteur accompagnant.
Pas de pré requis
Objectif du CACES® R485
Être capable d’utiliser en sécurité un chariot de manutention automoteur gerbeur à conducteur accompagnant
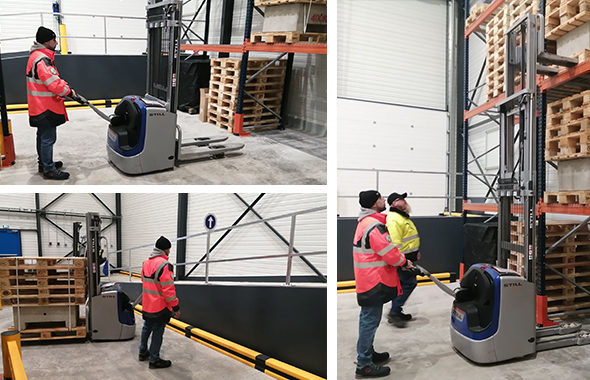
Durée du CACES® R485 :
Initial : 3 jours / Recyclage : 2 jours
Lieu de formation : Louviers - Dreux
Le CACES® R485 concerne les 2 catégories de gerbeurs à conducteur accompagnant suivantes :
Nota : La hauteur de levée est mesurée entre le sol et le dessus des bras de fourche dans leur position la plus élevée, c’est-à-dire avec le tablier en butée haute et - le cas échéant - le levage « transpalette » des bras supports totalement déployé.
• Catégorie 1 : Gerbeurs automoteurs à conducteur accompagnant (1,20 m < hauteur de levée ≤ 2,50 m)
• Catégorie 2 : Gerbeurs automoteurs à conducteur accompagnant (hauteur de levée > 2,50 m)
A noter : Dispenses de CACES® R. 485 : la détention du CACES® R485 de catégorie 2 permet d’autoriser la conduite des gerbeurs a conducteur accompagnant de catégorie 1.
Equipements concernés du CACES® R485
Les équipements visés par cette recommandation sont les chariots automoteurs gerbeurs à conducteur accompagnant au sens du couple de normes européennes harmonisées EN ISO 3691-1 : 2015 + EN 16307-1+A1/2015
➜ Véhicule ayant au moins trois roues, muni d'un mécanisme d'entrainement motorisé, à l’exception de ceux qui roulent sur rail, conçu pour transporter, lever, gerber ou stocker en casiers toutes sortes de charges et conduit par un opérateur circulant à pied avec le chariot.
Les CACES® R485 concernent uniquement les chariots gerbeurs à conducteur accompagnant à mât muni de bras de fourche dont les mécanismes de translation et de levage sont motorisés.
Rappel du contexte réglementaire du CACES® R485 :
Tout travailleur amené à utiliser un chariot de manutention à conducteur accompagnant doit avoir reçu une formation adéquate (art. R.4323-55 du Code du travail).
Il est en outre recommandé qu'il soit titulaire d'une autorisation de conduite délivrée par son employeur selon les modalités définies à l'article 3 de l'arrêté du 2 décembre 1998.
Le respect de ces prescriptions impose donc :
- que le conducteur ait reçu une formation spécifique et adaptée à la conduite en sécurité du chariot de manutention concerné, formation qui doit être complétée et réactualisée aussi souvent que nécessaire ;
- que son aptitude médicale à la conduite de cet équipement ait été vérifiée ;
- qu'il dispose des connaissances et du savoir-faire pour la conduite en sécurité du chariot de manutention concerné, attestés par la réussite aux épreuves théoriques et pratiques appropriées ;
- que son employeur se soit assuré qu'il a connaissance des lieux et des instructions à respecter sur le ou les sites d'utilisation ;
- que son employeur lui ait délivré une autorisation de conduite pour le chariot de manutention concerné.
Obligations de formations du CACES® R485
Tout conducteur de chariot de manutention automoteur doit avoir bénéficié d’une formation à la conduite dont la durée et le contenu doivent être adaptés compte tenu de son expérience pratique de la conduite et de la complexité de l’équipement de travail concerné.
Cette formation est rendue obligatoire par l’article R.4323-55 du Code du travail. Ses modalités sont définies à l’article 1 de l’arrêté du 2 décembre 1998 pris en application de cet article.
Le salarié doit, au terme de cette formation dispensée en interne ou organisée dans un organisme de formation spécialisé, disposer des connaissances théoriques et du savoir-faire pratique nécessaires à sa conduite en sécurité. L’objectif de la formation est notamment :
➜ de lui apporter les compétences nécessaires à la conduite du chariot concerné en situation de travail
➜ de lui transmettre les connaissances théoriques et le savoir-faire pratique nécessaires à la conduite en sécurité du chariot concerné,
➜ de lui communiquer les informations relatives aux risques liés à son utilisation,
➜ de lui permettre de maîtriser les moyens et méthodes permettant de prévenir ces risques
Une simple « formation au passage du CACES® », qui se limiterait à préparer le salarié à répondre aux questions du test théorique et à reproduire les gestes qui lui seront demandés lors des épreuves pratiques, ne suffit pas à remplir ces obligations réglementaires essentielles pour la prévention des risques.
Pour se présenter au test CACES® le candidat doit présenter une attestation, établie par un organisme spécialisé ou par son employeur, mentionnant qu’il a bénéficié d’une formation lui permettant a minima de disposer des connaissances théoriques et du savoir-faire pratique.
Exemple d'attestation à destination des employeurs. Lorsque l’OTC réalise consécutivement la formation requise ci-dessus et le test CACES® correspondant, il n’est pas tenu de délivrer physiquement l’attestation avant le déroulement des épreuves. Il doit toutefois être en mesure de l’éditer sur demande
Programme de votre formation CACES® R485 (Chariot Conducteur Accompagnant)
A - Connaissances théoriques
➜ Rôle et responsabilités du constructeur / de l’employeur (conformité du matériel, notice d’instructions, formation, autorisation de conduite, aptitude médicale, vérifications réglementaires, vérification et entretien du matériel...),
➜ Dispositif CACES® (rôle de l’Assurance Maladie, recommandation...),
➜ Rôle et responsabilités du conducteur (devoir d’alerter, droit de retrait...),
➜ Connaissance des différents acteurs internes et externes en prévention des risques professionnels concernés.
➜ Alimentation en énergie électrique des gerbeurs, différents types de batteries,
➜ Terminologie et caractéristiques générales (hauteur, levée libre, portée, capacité),
➜ Différentes technologies de batteries d’accumulateurs – Intérêt des batteries gel ou lithium pour la sécurité,
➜ Identification, rôle et principes de fonctionnement des différents composants et mécanismes, notamment de translation et d’élévation,
➜ Identification, rôle et principe de fonctionnement des différents organes et dispositifs de sécurité – Risques liés à la neutralisation de ces dispositifs,
➜ Equipements de préhension de charges disponibles pour les gerbeurs, leurs utilisations possibles,
➜ Paramètres de fonctionnement ajustables par un technicien spécialisé en fonction des conditions d’utilisation (vitesse maximale, rampes d’accélération et de freinage...),
➜ Intérêt de l’option de mise à hauteur automatique des bras de fourches (sur certains modèles de gerbeurs).
➜ Caractéristiques et spécificités des différents types de chariots de manutention :
• gerbeurs à conducteur accompagnant concernés par la recommandation R485,
• transpalettes et gerbeurs ≤ 1.20 m concernés par la recommandation R.366 et la recommandation régionale n°2 de la Carsat Centre-Ouest (3CTACA),
• chariots à conducteur porté concernés par la recommandation R.489,
• chariots tout-terrain concernés par la recommandation R.482,
• autres chariots de manutention.
➜ Catégories de CACES® R485 pour les gerbeurs à conducteur accompagnant.
➜ Évaluation de la masse et de la position du centre de gravité des charges habituellement manutentionnées, selon le lieu et l’activité,
➜ Conditions de stabilité (moments, renversement, basculement...)
➜ Conditions d’équilibre du chariot,
➜ Facteurs qui influent sur la stabilité latérale (renversement) et longitudinale (basculement), durant les manutentions et pendant les déplacements,
➜ Lecture de tableaux et d’abaques de charge (charge maximale en fonction de la position du centre de gravité de la charge, de la hauteur de levage...),
➜ Positionnement approprié de la charge sur le porte-charge.
➜ Principaux risques - Facteur(s) de risque et moyens de prévention associés :
• renversement latéral du gerbeur (dévers, sol en mauvais état, translation charge haute, vitesse excessive en courbe...),
• basculement du gerbeur vers l’avant (pente, surcharge, translation charge haute...),
• chute du chariot depuis un quai (pont de liaison défaillant ou mal positionné, mouvement du camion...), un hayon (surcharge, absence ou défaillance des butées...), une rampe...
• renversement de la charge au sol ou sur un piéton,
• chute de la charge lors de la dépose (mauvais positionnement sur les lisses du palettier),
• ruine de tout ou partie d’un palettier (surcharge de lisse, détérioration d’échelle, soulèvement de lisse dû à l’absence de clavette...),
• heurts de personnes ou d’engins,
• chute de plain-pied lors de la translation, notamment en cas de heurt d’un obstacle en reculant sur un sol encombré,
• chute de hauteur du conducteur (quai, hayon...),
• écrasement / coincement d’une partie du corps (main, pied...) du conducteur entre un obstacle et le châssis, le timon, les roues... lors de manœuvres sur un site exigu ou dans des passages trop étroits,
• heurt d’un obstacle en hauteur (poutre, linteau, sprinkler, dispositif d’éclairage...),
• risques liés au manque de visibilité (défaut d’éclairage, charge masquant la visibilité...),
• risques liés à la mise en œuvre des batteries d’accumulateurs (brûlures au contact de l’acide, modalité de réalisation des opérations courantes (connexion / déconnexion, manipulation, mise en charge...),
• risques liés à l’utilisation des énergies mises en œuvre (mécanique, électrique, hydraulique...),
• risques de TMS (lombalgie...) liés notamment à l’absence de mise à hauteur des palettes lors des manutentions manuelles,
• risque d’incendie / explosion (en particulier de la batterie / du chargeur).
➜ Repérage de ces risques potentiels, sur le trajet à parcourir et lors des opérations à effectuer,
➜ Transport et élévation de personnes : connaître les interdictions (élévation sur les bras de fourche...), savoir expliciter et justifier les applications autorisées.
➜ Identification des différents types de palettes et contenants existants en fonction de leurs caractéristiques, connaissance de leurs limites d’emploi,
➜ Fonctionnement, rôle et utilité du dispositif automatique de mise à niveau des bras de fourche,
➜ Vérification de l’adéquation des paramètres de fonctionnement ajustables (vitesse maximale, rampes d’accélération et de freinage...) aux conditions d’utilisation,
➜ Positionnement du conducteur par rapport au gerbeur dans les différentes situations d’utilisation (translation, pente, gerbage / dégerbage, sur un hayon, dans un véhicule...),
➜ Conduite à tenir en cas d’incident ou de défaillance sur le gerbeur (panne, incendie...) ou la charge (renversement, épandage accidentel de marchandises...),
➜ Justification du port des EPI en fonction des risques liés à l’opération à réaliser,
➜ Consultation et utilisation de la notice d’instructions du constructeur,
➜ Interprétation des pictogrammes de manutention sur les charges,
➜ Interprétation des pictogrammes relatifs aux risques chimiques, biologiques et bactériologiques,
➜ Interprétation des panneaux de circulation,
➜ Plan de circulation, consignes de sécurité, protocole de chargement / déchargement : exploitation de ces documents, intérêt de ces informations pour le cariste,
➜ Effets de la conduite sous l’emprise de substances psycho-actives (drogues, alcool et médicaments),
➜ Risques liés à l’utilisation d’appareils pouvant générer un détournement de l’attention (téléphone mobile, diffuseur de musique…)
➜ Justification de l’utilité des vérifications et opérations de maintenance de premier niveau qui incombent au conducteur, réalisation pratique de ces tâches,
➜ Principales anomalies concernant :
• les chaînes et mécanismes de levage,
• le circuit hydraulique,
• les organes de freinage et de direction,
• les bandages
• etc…
B – Savoir-faire pratiques
➜ Utilisation des documents suivants : notice d’instructions (règles d’utilisation, restrictions d’emploi...) et rapport de vérification périodique (validité, observations, restrictions d’usage, signification du macaron apposé par l’organisme...),
➜ Vérification visuelle de l’état du gerbeur (châssis, roues, mât, charpente, jupe, capot de batterie...) afin de déceler les anomalies et d’en informer son responsable hiérarchique,
➜ Vérification du fonctionnement du gerbeur (translation, direction, élévation...),
➜ Vérification du bon fonctionnement des organes et dispositifs de sécurité (sécurités de timon haute / basse et inversion de sens de marche, arrêt d’urgence, dispositif de condamnation, freinage, éclairage, avertisseur sonore, dispositifs de signalisation sonores ou lumineux, protecteurs...)
➜ Vérification du branchement et de la charge de la batterie d’accumulateurs,
➜ Vérification de l’adéquation des paramètres de fonctionnement du chariot (vitesse maximale, rampes d’accélération et de freinage...) aux conditions d’utilisation,
➜ Vérification de l’adéquation du gerbeur aux opérations de manutention à réaliser (charge à manutentionner, distance de son centre de gravité, capacité effective du chariot et de son équipement de préhension de charges, hauteur de levage...).
Nota : Cette opération ne doit pas être confondue avec l’examen d’adéquation requis par l’arrêté du 1er mars 2004, relatif aux vérifications des appareils et accessoires de levage, qui relève de la responsabilité du chef d’établissement.
➜ Manœuvrer et diriger le gerbeur, en marche avant et arrière, en ligne droite et en courbe, à vide et en charge...
• adopter une position latérale au timon adaptée à la manœuvre en cours,
• regarder dans le sens de la marche pour conserver une bonne vision du parcours, y compris avec une charge limitant la visibilité,
• regarder en arrière lors du recul pour s’assurer de l’absence d’obstacle au sol, veiller à la stabilité de la charge,
• veiller à la stabilité de la charge,
• veiller à la sécurité des piétons éventuels (croisements d’allées, portes...),
• orienter le gerbeur dans le sens approprié et adapter sa vitesse en pente.
➜ Pour chaque manutention, contrôler au moyen de l’abaque ou du tableau des charges que la manutention est possible compte tenu de la capacité effective, de la hauteur de levage et de l’équipement porte-charges dont le gerbeur est équipé.
➜ Prendre et déposer une charge au sol
• évaluer la position du centre de gravité de la charge,
• positionner le gerbeur pour effectuer la prise,
• prendre la charge de manière à en assurer l’équilibre,
• s’assurer que le lieu de dépose est approprié,
• déposer la palette avec précision à l’endroit déterminé.
➜ Effectuer le gerbage et le dégerbage de charges en pile
• apprécier le nombre maximal de niveaux sur lesquels les charges peuvent être empilées sans écroulement ou basculement de la pile,
• positionner le gerbeur face à la pile pour effectuer la prise / la dépose,
• prendre / déposer une charge sur une pile sans en compromettre la stabilité
➜ Effectuer le stockage / le déstockage à tous les niveaux d’un palettier
• localiser l’emplacement de stockage selon des instructions reçues,
• apprécier les risques liés au stockage / déstockage à cet emplacement (en particulier état des lisses et présence des goupilles anti-soulèvement),
• vérifier le bon état du support de charge (palette...) et la qualité de son conditionnement (stabilité, banderolage...),
• positionner le gerbeur face à l’emplacement de stockage,
• prendre / déposer la charge dans l’alvéole
➜ Réaliser le chargement et le déchargement d’un véhicule à quai par l’arrière
• s’assurer que toutes les conditions permettant le chargement / le déchargement sont remplies, notamment immobilisation et/ou calage pour interdire le départ inopiné du camion (protocole de sécurité),
• vérifier que le gerbeur est adapté, compte tenu du gabarit du véhicule, de la résistance du plancher, de la présence des raidisseurs latéraux...,
• mettre en œuvre les dispositions et moyens permettant un accès en sécurité à la plate-forme du véhicule (niveleur correctement positionné, pont de liaison adapté et immobilisé...),
• recourir, le cas échéant, à un système d’éclairage adapté à l’intérieur du véhicule ou sur le gerbeur,
• adapter la vitesse et la trajectoire du gerbeur à l’entrée, à la sortie et à l’intérieur du véhicule,
• prendre / déposer les charges conformément au plan de chargement, en optimisant la répartition des charges dans le volume utile
➜ Effectuer le chargement et le déchargement d’un véhicule au moyen d’un hayon
• s’assurer que toutes les conditions permettant le chargement / le déchargement sont remplies, notamment immobilisation et/ou calage pour interdire le départ inopiné du camion (protocole de sécurité),
• s’assurer que la CMU du hayon est appropriée aux poids cumulés du gerbeur et des charges à manutentionner, puis vérifier l’état et le fonctionnement du hayon (dispositifs de sécurité, butées escamotables...) ainsi que la présence des documents requis (rapport de vérification périodique du hayon...
• vérifier que le gerbeur est adapté, compte tenu du gabarit du véhicule, de la résistance du plancher, de la présence des raidisseurs latéraux…
• mettre en place une signalisation adaptée pour prévenir les risques liés à la circulation des véhicules et piétons au voisinage du hayon,
• recourir, le cas échéant, à un système d’éclairage adapté à l’intérieur du véhicule ou sur le gerbeur
• adapter la vitesse et la trajectoire du gerbeur à l’intérieur du véhicule,
• prendre / déposer les charges conformément au plan de chargement, en optimisant la répartition des charges dans le volume utile
➜ Manutentionner une charge longue, un conteneur rigide contenant un liquide et une charge déformable (sac, big bag...)
• pour chaque cas, définir une méthode de prise et de manutention permettant d’assurer la stabilité de la charge (flexibilité, glissement...),
• prévoir et mettre en œuvre les dispositions et les moyens adaptés.
➜ Adapter sa vitesse en fonction de la charge, de la nature du sol et du trajet à effectuer,
➜ Dans la zone d’évolution, identifier les sources potentielles de risques liés à la circulation et à la stabilité de la charge ou du chariot, et choisir un parcours adapté,
➜ Stationner et arrêter le gerbeur en sécurité
➜ Effectuer les opérations d’entretien journalier,
➜ Vérifier les différents niveaux et identifier les manques éventuels, faire l’appoint si nécessaire et mettre le gerbeur en charge,
➜ Rendre compte des anomalies et dysfonctionnements.
Validation
Cette formation donnera lieu à la remise d’une attestation de présence et d’une évaluation dans les conditions définies par la Recommandation CACES® R485 permettant à l’employeur de décider ou non d’établir et délivrer une autorisation de conduite à son salarié
MODELE D’AUTORISATION DE CONDUITE
Modalité d’évaluation du CACES® R485
QCM et examen pratique selon le schéma :
• Prise de poste.
• Réalisation d’une tâche.
• Fin de poste.
Délai d’accès au CACES® R485
Le CFB s’engage à vous répondre sous 48h maximum.
Nous envisagerons la date de début de formation en fonction de vos besoins, de votre mode de financement et de notre calendrier de formation.
6 bonnes raisons de choisir le CFB pour votre CACES® R485 :

1. Notre Accueil
Nous vous garantissons un accueil téléphonique et physique personnalisé de qualité.

2. Notre infrastructure
Au cours du second trimestre 2015, le CFB, situé en bordure de la nationale 12, disposera d’une aire technique de 900M² (dont une partie couverte) qui sera uniquement dédié à la formation CACES.

3. Notre suivi pédagogique
Vous serez encadré par un formateur ayant de l’expérience dans l’utilisation des grues auxiliaires.

4. Notre organisation
La formation se déroule par petit groupe sous forme d’atelier. Cette organisation optimise le temps de formation réel.

5. Formateur
Vous serez encadré par un même formateur afin d’assurer un excellent suivi de votre formation.
Financements :
Salariés, demandeurs d'emplois ou entreprises, des sources de financements sont à votre disposition.
Nous vous accompagnons pour constituer votre dossier de financement.
Contactez-nous pour en savoir plus au 02 37 46 81 07.
Accessibilité
Les personnes en situation de handicap souhaitant suivre cette formation sont invitées à nous contacter.